Europa es el principal productor y exportador de aceite de oliva. Solo en España se dedican 2,5 millones de hectáreas al cultivo de olivo. Jaén es un caso excepcional, está cubierto por un inmenso manto de olivares que, como pompones verdes, engalanan el 85% de la superficie cultivada. Esta industria es una importantísima fuente de riqueza, sin embargo aún puede aportar más beneficios si los residuos de la poda se transforman en recursos, algo a lo que está contribuyendo la investigación en ciencia de materiales y los principios de la economía circular.
Cada año en Europa se producen siete millones de toneladas de residuos procedentes de la poda del olivo. La mayor parte se quema, lo que contribuye a las emisiones de CO2, y otra parte se devuelve triturada al terreno, lo que puede favorecer la propagación de plagas. En la actualidad se ha puesto en marcha un proyecto con el que transformar los residuos leñosos de la poda en recursos de gran valor, creando biocomposites para el sector de la automoción y el mobiliario que mejoran las propiedades tecnológicas y el impacto medioambiental de los plásticos originales.
Los biocomposites son materiales compuestos, es decir, una mezcla de materiales con la que se busca mejorar las propiedades que tendrían por separado, tanto con respecto a su huella ecológica como en sus aplicaciones. Se llaman biocomposites poliméricos aquellos en los que al menos un constituyente procede de fuentes naturales (de ahí el prefijo bio) y cuya matriz está compuesta por polímeros. En este caso los residuos de la poda se convierten en fibras que se mezclan con una matriz polimérica de polipropileno (PP) y ácido poliláctico (PLA), dos plásticos respectivamente reciclados y reciclables.
Este proyecto de revalorización de la poda del olivo se llama Life CompOlive y comenzó en 2019 por iniciativa de Andaltec, el Centro Tecnológico del Plástico situado en Martos, Jaén; una localidad con una importante tradición industrial vinculada a la automoción. Cuenta con el apoyo del Centro Tecnológico del Olivar y del Aceite (Citoliva), de la Universidad de Jaén y de las empresas Plasturgia, Matricería Peña, Caliplast y Ford.
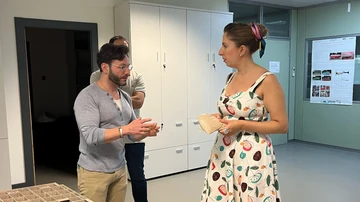
Hace un par de semanas visité las instalaciones de Andaltec y los científicos que trabajan allí me enseñaron emocionados los extraordinarios resultados del proyecto. El proceso comienza con la recolección de los residuos de la poda y su triturado. Estos se separan en función del tamaño, se tratan químicamente y se caracterizan para conocer la composición de la fibra –la cantidad de lignina, celulosa y hemicelulosa–. Según el tamaño de la fibra y su composición, se analiza su compatibilidad con la matriz polimérica, es decir, se evalúa qué tal se mezcla con el plástico y cómo cambian sus propiedades al integrarse todas las partes formando un composite. Para ello se fabrican unas probetas con el composite, que son unas piezas con una forma concreta que se pueden someter a ensayos de tracción y resistencia al impacto; es decir, se mide cuánta tensión soportan antes de romper, cómo de elástico es el material, cómo responde a la flexión, etc. Todos estos ensayos están tipificados, lo que permite comparar objetivamente unos materiales con otros. Además, se usan otras técnicas analíticas como la espectroscopía, la calorimetría y la microscopía que permiten conocer cómo se comporta el material según los cambios de temperatura y cómo le afectarían otras sustancias, como por ejemplo la humedad. Finalmente se seleccionan varios composites para cada caso industrial, ya que no se necesitan las mismas propiedades para fabricar el salpicadero de un coche que la defensa o el reposapiés, o un mueble de interior que uno de exterior. Pude tener en mis manos varios de los prototipos industriales.
Una vez seleccionados los composites de interés, estos se fabrican en formato pellet, que son porciones del material del tamaño de granos de arroz. Este formato es el que se usa para alimentar la maquinaria industrial de inyección de plásticos, que es la que se utiliza para fundir el material y con un molde darle la forma final deseada. Por esa razón también es importante que el composite sea termoplástico, es decir, que se funda aplicando calor. Esa cualidad lo convierte en un material reciclable, ya que se puede trocear y fundir una y otra vez.
Este nuevo material resuelve varios problemas además del obvio de la gestión sostenible del residuo de la poda del olivo. Por un lado, al transformar un residuo en un recurso, se convierte un gasto en una nueva fuente de ingresos para el sector agrícola. Por otro lado ofrece una solución a la directiva europea que demanda incorporar materiales reciclados y reciclables al sector de la automoción. Además, este biocomposite se puede integrar en la cadena de fabricación sin necesidad de cambiar la maquinaria, ya que se puede usar en las mismas extrusoras e inyectoras de plástico convencional.
El resultado es un material de alto valor ecológico. Para evaluar el impacto medioambiental de cualquier material se debe calcular su ACV (análisis de ciclo de vida) que consiste en medir la huella ecológica de un material a lo largo de todas las etapas, desde la extracción de la materia prima hasta el final de su vida útil. En este caso, no se plantarían olivos para fabricar el biocomposite (algo de lo que no pueden presumir todos los materiales biobasados) sino que la materia prima es un residuo que se produce en abundancia, en una cantidad suficiente como para abastecer la demanda. Además, la matriz polimérica también es más sostenible que un plástico virgen de origen fósil, porque el PLA puede proceder de fuentes naturales y ser reciclable, y el polipropileno es reciclado, así que todos los materiales que componen el biocomposite reducen su impacto medioambiental en comparación con los materiales que vienen a sustituir.
El proyecto Life CompOlive es un magnífico ejemplo de I+D+i en ciencia de materiales, de economía circular y de colaboración público-privada de una región. Los hallazgos de este proyecto sin duda se acabarán incorporando a otras industrias en las que se utilicen materiales plásticos de media y larga duración, como la construcción o el envasado. Con este proyecto han logrado darle la vuelta a la situación, convirtiendo un problema medioambiental en una solución, y un problema de gestión de residuos de la agricultura en una fuente de ingresos de la que se beneficiarán diferentes sectores. Esto ha sido posible gracias a la ciencia de materiales, un campo de investigación multidisciplinar en el que colaboran químicos, ingenieros y físicos; gracias al conocimiento del mercado automovilístico y mobiliario; gracias a integrar los principios de la economía circular a un caso real, y gracias a una concepción inicial del proyecto como modelo de negocio, rompiendo así la frontera entre lo que sucede dentro del laboratorio y lo que de verdad se demanda fuera de él.